London Airport Server Room Emergency
The Challenge
A major London airport had contacted Celsius Hire for a temporary cooling solution for their vital server rooms. The client was aware their cooling systems needed maintenance and replacement so had booked for Celsius Hire for their planned maintenance.
The timing of this project was incredibly lucky as we installed for planned works with the system being completed, filled and tested without load before a planned staged handover.
However, the clients system failed 3 days prior to our commissioning date. Luckily we had already installed and heat load tested so an emergency call meant we could get the system up and running over the phone within 30 minutes whilst the room temperatures were rising, with our engineer Chris Brown arriving 1 1/2 hours after initial phone call.
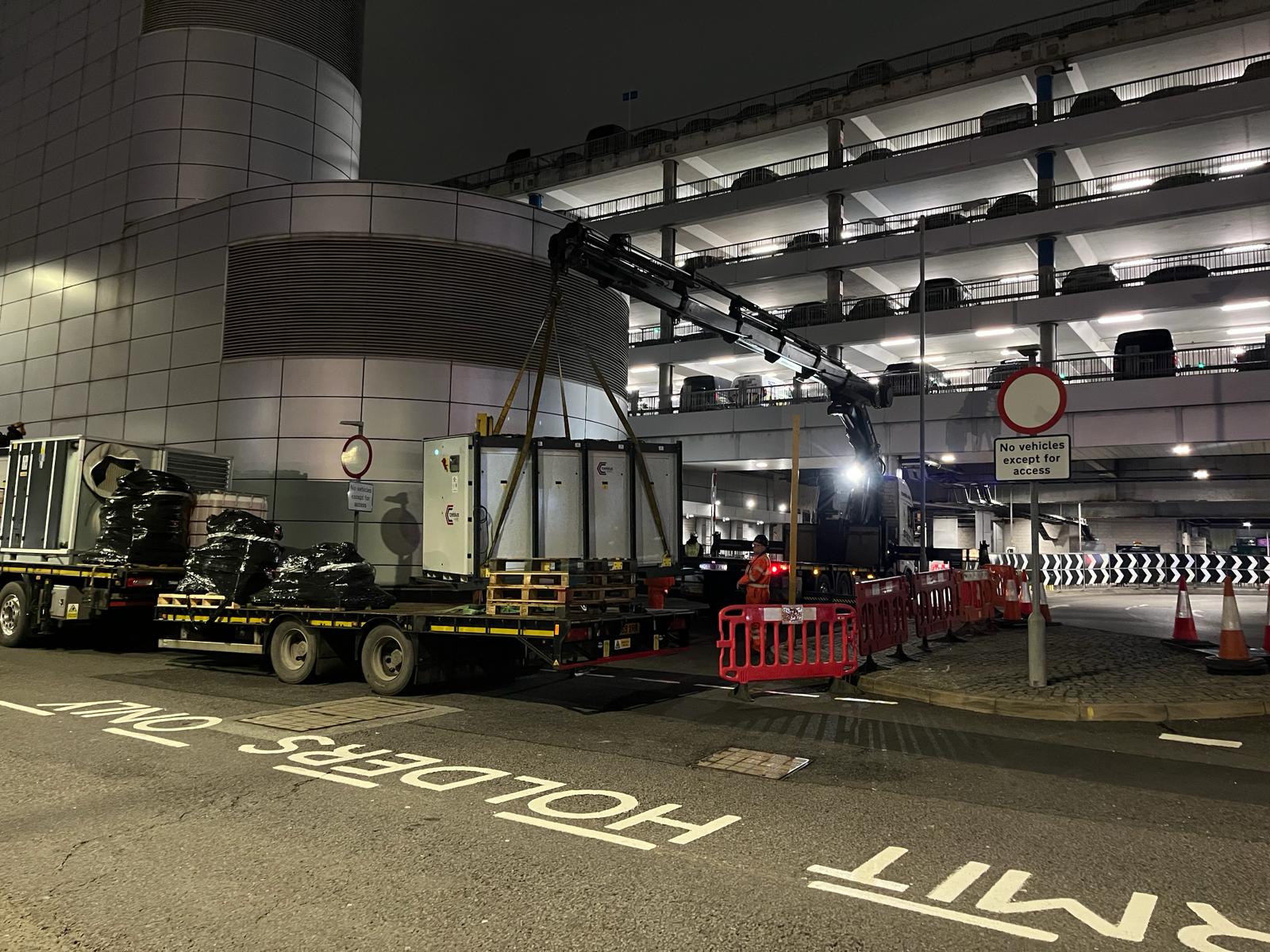
The Solution
A site survey concluded we could provide the required duty using our 125KW chiller package for this data centre cooling refit project.
We specified that a AHU and generator package would also be appropriate for this site.
Delivery and Installation
Being a busy London Airport we had our hiab delivery of the hire equipment starting at 11pm, through to 3am. We opted for these times due to road closures and traffic management required, causing minimum disruption. Pallet trucking AHU’s down service lift to the underground data room. Additionally we added a long pipe run down through a riser and fixed up at a high level using MEWPs (mobile elevated work platforms), with additional pumps installed to overcome pressure drops of the pipe runs.
Data Centre Cooling Hire Equipment
- 2 x 125KW Chillers
- 2 x 150KW AHUs
- 125m e/w pipe run
- 500m total hose
- 2 x 150kVA Generator Packages
The Result
We met sites requirement by matching their existing cooling duty, including additional backup with an N+1 set up, to ensure further backup should anything fail. In addition to a generator package to ensure power was met at all times whilst work was being carried out for the refurbishment.
“System running and holding temperatures allowing client to carry out essential repair works on their existing equipment to prevent future issues and down time. We had a lucky situation with the equipment being installed and ready to go prior to an unexpected failure, ahead of the planned maintenance, which saw the team jump into action and get the sites cooling back up and running in an incredibly small time frame.” – Sean Johnson, Senior Sales Engineer